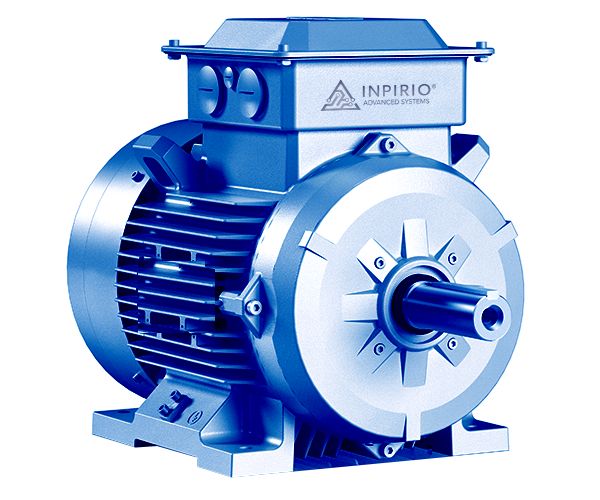
Generators are designed for direct or indirect coupling to the water turbine and to meet all requirements of small hydro power plants, medium or big hydro power plants.
Modular design enables usage of standard and well proven subassemblies such as bearings, exciter, Permanent Magnet Generator (PMG), rotating rectifier, frames, coolers and fans thus resulting in shorter engineering and delivery time, as well as simplified installation and reduced startup time since the generators are fully tested in the factory and delivered at site already assembled
STANDARDS
All our electrical machines are in full conformity with IEC and ISO standards and VDE recommendations. They can also be manufactured in accordance to other standards and requirements in respect with customer’s requests
Stator
- Core made of high quality silicone dynamo steel sheets
- Three-phase star connected armature winding on stator
- Double layer armature winding made of electro-technical rectangular copper wire, insulated with enamel varnish and glass
- Individually formed coils
- High voltage generators insulated with porous mica tape
- Vacuum pressure impregnation
Rotor
- Core made of high quality silicone dynamo sheets or high quality steel plates
- Field and damper winding on rotor
- Field winding made of electro-technical rectangular copper wire, insulated with enamel varnish and glass
- Damper winding made of round copper bars, short circuited with copper end plates
- Thermal class insulation F (H on request) with temperature rise in class B
- Brushless excitation with exciter, diode rectifier provided with varistors for overvoltage protection
- Depending on requirements, generators can be designed with Permanent Magnet Generator which enables generator black-start as well as the supply of the AVR power input
- Designed and tested for the required runaway speed
Degree of protection and cooling system
- open air circulation system
- Totally-enclosed closed air-circulation system – built-in air to water heat exchanger(s)
- Terminal boxes
Shaft and coupling
- Shaft end is adopted to direct or indirect coupling, according to IEC 60034-7
- Shaft end(s) according to turbine requirements
- Flywheel on shaft as an option
Paint finish
- Standard paint finish
- Paint binders in accordance
- Other colours or special paint finishes on REQUEST.
Main terminals
- Winding ends brought out to terminal box(es)
- Cable entry plate made of non-magnetic material supplied on request (with or without cable glands
Direction of rotation
- Rotor rotates clockwise or counterclockwise according to request
- Right sequence of phases
Bearings
- Roller grease lubricated bearings •
- Sleeve oil lubricated bearings – end-shield or pedestal •
- Sleeve bearings are cooled by ambient air, integrated water coolers or external oil lubrication • External oil supply system is offered as an option •
- Built-in equipment is agreed upon with the customer
Vibration stability
- Statically and dynamically balanced in factory
- Vibrations measured in factory are within the permissible limits
Noise level
- Noise damper on request
Radio interference suppression
- Complies with grade N of VDE 0875
Unbalanced load
- Rotor’s damper winding designed for parallel operation and unbalanced load at nominal current in one or two phases according to IEC 60034-1
Overload
- 1,5 times the rated current at least 30s
Final tests and measurements on fully assembled generators in the factory
Check-up of mechanical dimensions
Insulation resistance of generator and exciter
Mechanical run
No-load losses and characteristic
Short-circuit losses and characteristic
Determination of efficiency
Heating test
Vibration measurement
High-voltage test
Overspeed test – 2 min
Direction of rotation
Bearing’s temperature measurement
Check of built-in equipment
Upon request other tests can be performed on fully assembled generator.
Tests and measurements during production in the factory
Magnetization test and hot spots check
Winding’s ohmic resistance of generator and exciter
Tests on stator coils
Tests on wound stator
Tests on rotor winding
Tests on wound rotor
Weld check
NDT test of bearings
Pressure test on heaters
Upon request other tests can be performed in all phases prior to generator assembly.